During a job interview, asking candidates specific questions that help gauge their skills and knowledge relevant to the role is typical. When interviewing for an Inventory Controller position, the interviewer also poses questions that specifically test the candidate’s expertise in inventory control and management.
In this article, we will see frequent Inventory Controler Interview questions and answers, which will give you an idea of how to prepare.
Preparing for an Inventory Controller Interview
Before appearing for the interview, you have to understand the interviewer’s expectations. It means you should be ready with the sharpened skills the interviewer seeks. You should be aware of the employer’s company work environment.
Preparing for an inventory controller interview involves research and practice. Familiarize yourself with the company and its industry, understanding its inventory control needs and challenges. Brush up on inventory management concepts and terminology. Review common interview questions and practice formulating structured and concise responses.
The more your experience and skill set matches the requirements, and the more you surprise them with Inventory Controller knowledge, the higher the chance you will get hired. In this, the following Inventory Control job-related questions and their answers will help you.
Inventory Controller Interview Questions
Here are some sample interview questions and their answers for inventory Controller roles to help you when preparing:
What was your work and contribution in your previous job?
My work was to ensure all inventory levels and their records are adequate. I faced many challenges in my previous job, such as inexperienced staff and needing management procedures and SOPs. So, I fixed all those issues with my superior’s help one by one.
I created basic floor operation procedures and record keeping easier for inexperienced staff. Inventory management operations started working smoothly while the staff was trained with time, and the management system also improved.
What is the last improvement you made to an inventory management process?
Before I left my last job, I contributed to creating an improved BOM (bill of material) prediction system. Since my job was in a production company, my most important job was to keep an adequate buffer stock of raw materials. But, the problem was with low shelf life ingredients. So, I improved the inventory management process by creating automated forecasting and a BOM calculator highly compatible with variable production demands.
What challenges did you face during your last job and how did you manage them?
The major challenge I faced in my last job was training my replacement (alternative for the same job) along with doing multiple jobs left by vacant positions. I played multiple job positions such as data entry operator, storekeeper, inventory controller, purchase assistant, production coordinator, and staff coordinator at the same time.
Fortunately, I was able to complete all tasks by using the sort and executing the technique. It improved my time management and quick response skills to a great extent.
Can you please describe briefly your experience?
I have a wealth of knowledge of this industry, and this puts me at a much better chance of achieving success in my job. I began my career as a warehouse employee, assigned to offload and arrange new stock, in addition to relocating the items to customers. I was in close contact with the manager of inventory, who would instruct me on what I should do.
Later I took a class in the management of inventory, which made me go from an offloader in a single position to an employee in the department of inventory. I’ve since worked for three different businesses that handle different kinds of inventory and have acquired the tools I require to do well in my job.
Had you negotiated with the supplier for a better deal and how?
In my previous position, one supplier continually charged us too much for their products. After discussing it, they told me that the size of our order needed to be more to qualify for their pricing tier, which was lower. Therefore I joined my team to boost our monthly orders by 10% so that we could be eligible for the lower pricing price. This helped us save thousands of dollars every month.
What will you investigate if the inventory didn’t match the records?
If there was a difference between the inventory in hand as well as sales data, I’d first examine the period the discrepancy took place. If the discrepancy was observed over a prolonged period, it could result from an error by a human or a glitch in the system. However, if the issue was only present for a single day, the chances are that someone stole from the business. In either event, I’d immediately notify my supervisor so that they could begin an investigation.
What will you do if you receive half-damaged goods from the supplier?
One of my most important duties is ensuring quality assurance and maintaining good vendor relations. This must be balanced by protecting the best interests of the company. I’d document the event with photos or precise descriptions.
If the supplies were in demand, I’d contact the supervisor and find the right supplier to temporarily meet the demand. At the same time, I worked out the problem with the supplier previously in charge. I’d then identify when the damage occurred and, based on the outcomes, return the items to be replaced. But, I generally suggest that management search for a better supplier for future incidents.
We want to ensure that our inventory is always at the right level. What is the ideal inventory level for each product?
In my previous position, I was required to determine what items we should keep on hand at all times. We employed a formula that included customer demand as well as sales history and lead time to determine the best quantity of inventory for each product. This allowed us to ensure that we had sufficient stock of our most sought-after items in stock while conserving money by not having surplus stock.
Describe your experience with inventory audits.
“I’ve not been involved in an audit of inventory prior but I’m excited to learn more about the procedure. In my previous job in the capacity of an inventory controller, we performed an inventory count at least every 6 months. Barcode scanners were used to scan every product’s barcode and track its location in our inventory software. We took two days to finish the count .”
What techniques do you use to ensure a consistent supply of stock?
I do apply different inventory management techniques based on the nature of inventory items. You can call it a hybrid or mixture type. I will use JIT (just in time) for sourcing highly space-consuming but short delivery time items. Supply of Items with expiry and delayed delivery will be ensured by maintaining safety buffer stock.
CI will apply FIFO to consumable ingredients for production, so no expiring stock lags behind. High-value or high transportation-cost items are ordered using EOQ (economical order quantity). I will make relations with multiple vendors so another supply can be called in case of a problem with the first one.
What inventory management software are you familiar with?
I am familiar with some entry-level and advanced inventory management software. My first inventory management experience was with Tally ERP which I mastered in little time. Then at my previous job I worked on Sybase Database-based custom-built ERP system. Meanwhile, I have learned about inventory management in SAP and NetSuite also.
Can you describe what ABC analysis is and how you would use it?
In the field of materials control, ABC analysis is a method of categorizing inventory. ABC analysis is a method of dividing an inventory into three categories–“A items” that have very strict control and precise records. “B items” with less tightly-controlled and have poor records, and “C items” have the least control feasible and only a few records.
I will list all inventory items then I will categorize all of them into three categories A, B, and C. So different inventory management approaches will be used while ordering materials from those categories.
Tips to Ace Interviews for an Inventory Controller Position
Here are some useful strategies to aid you in your preparation for interviews with inventory control:
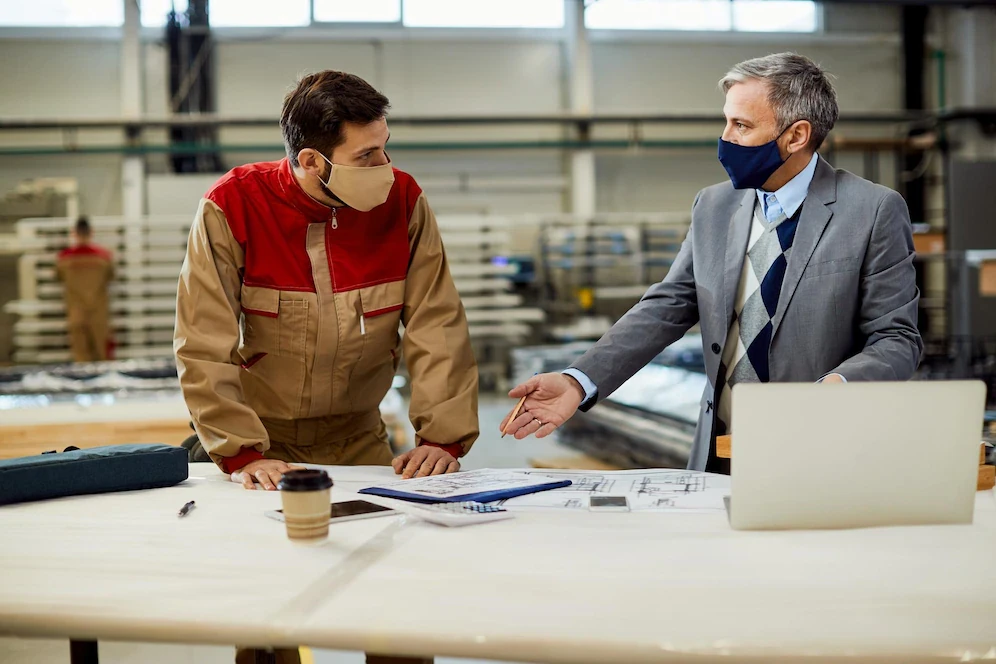
As a candidate seeking the position of inventory controller, it is crucial for you to possess expertise in effectively managing the supply chain to maintain optimal inventory levels for various businesses. Your role would involve coordinating stock levels, overseeing warehouse logistics, and accurately forecasting supply and demand requirements to ensure a consistent flow of inventory.
During the interview process, it is important for you to highlight your excellent communication skills and strong logistical mindset. Employers will be looking for candidates who can demonstrate exceptional coordination abilities and possess experience working with inventory management software. Make sure to emphasize your proficiency in these areas as they will be key factors in securing the position.
Remember, effective coordination and proficiency in utilizing inventory management software are vital for success in this role. Showcase your abilities and experience in these areas to stand out as a strong candidate for the inventory controller position. Good luck with your interview!