Inventory is invested working capital of the business. It is the most crucial part of any production-based business. Inventory is also termed as stock or material. And managing whole inventory-related tasks is Inventory Management Operation.
Businesses cant manage their capital without inventory control. Wrong management of inventory harms working capital and budget goals and thus business profit. Both understock and overstock situation affects damages business in some way.
So, Inventory control operations contain sophisticated procedures and tactics to avoid the chaos that could happen because of incorrect stock levels. Such as low level or unavailable stock halts production operation and on another hand excessive stock level can cause expiry, wastage, space limitation and budget failure.
Thus, inventory control operation includes inventory classification based on their nature and value. Classification of material affects inventory control productivity. Material can be managed by classifying them into adequate groups. Inventory controllers and store managers are in charge of these tasks.
What is the classification of Inventory?
Inventory is money. Even if you do not have a financial background, You should understand that inventory information in financial statements can be useful in the operation of your business.
A basic understanding of how inventory appears on the balance sheet and its impact on the income statement and cash flow statement will improve your ability to have the right item in the right quantity in the right place at the right time.
And, it starts from understanding the basic types of Inventory. The three basic types of inventory are
1. Raw Materials: raw materials inventories are ingredients or parts of the final product before we start actual production. (eg, meat and salt in burger product)
2. Work In Progress (WIP): work in progress inventory or unfinished products are materials entered into the production process but not yet completed. (eg, marinated chicken, sub-assemblies)
3. Finished goods: finished goods inventory or final product is completed goods ready to be sold to the end customer. (eg, Chicken Burger, Laptop)
Most inventories can be grouped under the above three categories. Yet the amount of each category depends on the nature of business and production. For example inventories in the distribution, and warehouse industries are different from those in manufacturing plants.
Distribution industries don’t keep raw materials. They simply classify inventories based on their final product type and buyer’s location. While manufacturing companies keep more raw materials and less finished goods. Mostly finished goods are temporarily stored and then quickly dispatched to resellers.
Classification of material in Inventory Control
The list of inventory types is not limited only to those 3 categories. The list can grow and it all depends on the nature of the business environment. Let’s have look at the following possible types of material in Inventory Control
- Raw Materials
- Packing Material Inventory
- Components
- Finished Inventory
- MRO Goods (Maintenance, Repair and Operations)
- Safety Buffer Stock
- Cycle Inventory
- Transit Inventory
- Excess Inventory
- Wasted/Defected Inventory
Benefits of Inventory Classification
Classification of material has a great impact on inventory control operations. Thus it helps to achieve business productivity which leads to good profits. Let’s see the benefits of inventory classifications.
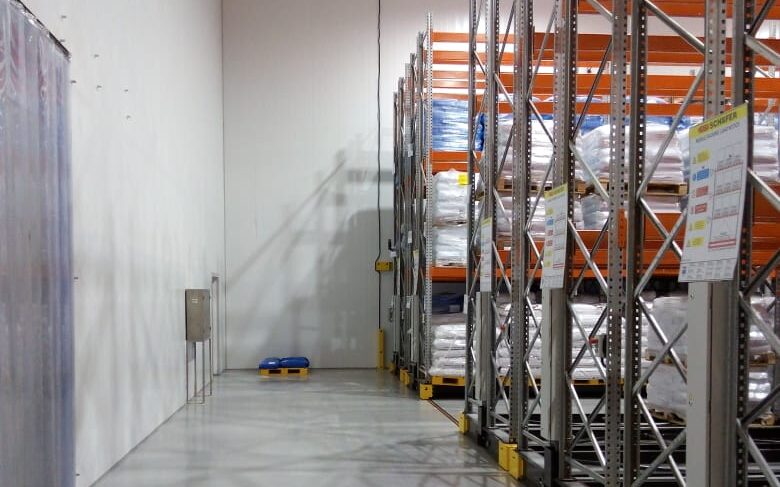
Better storage space management: Not all companies are lucky to have enough storage space on growth days. Most companies always struggle to manage floor space occupied by inventory items. Excessive stock occupies lots of space unnecessarily and creates problems for necessary stock items.
Storage cost is more significant when businesses use rented storage space. Classifying materials based on their expiry, need and reorder delivery time can help to decide JIT (just in time items) which helps to avoid long time space-occupying items to buy in advance.
Minimal working capital gets invested in material: Material can be analysed and classified using the ABC method. It allows for identifying excessive high-cost stock items. Then they can be purchased based on their minimal required stock levels without interrupting smooth production operations.
Increases Inventory Turnover Ratio: The inventory turnover ratio is how many times inventory is replaced over a period of time. A high average ratio means your inventory is getting quickly replaced and holds minimal capital. A low inventory turnover ratio means some of your inventory is holding large capital for a long period of time.
Lowers overall cost: Excessive inventory needs more space, handling, and maintenance costs. Take an example of frozen chicken stock unnecessarily stored in a cold store for more than six months. It requires money to keep cold storage running, and the risk of stock expiry is also overhead. And, what if we keep such stock only for a month. We can save space and money. Hence classifying materials in inventory control lowers overall business costs.
Example,
Let’s take the example of a chicken burger production company.
The chicken burger final product will need raw chicken, spices, packing material, wrapper bags, soya, rusk, bread crumbs etc
so we can classify all required materials in the following classes,
- Raw Material – raw chicken
- Ingredients – burger spice, oil, rusk, bread crumbs, soya
- Work in progress – flaked chicken, a mixture of chicken, soya, spice
- Packing material – burger paper, product wrapping bag, product duplex box, FG carton
- Finished goods – packed burger patties in FG carton.
Conclusion
Inventory is the lifeblood of every type of industry. Excess or shortage of inventory is harmful to the business. Classification of inventory helps to manage material properly. It reduces unnecessary costs and working capital.